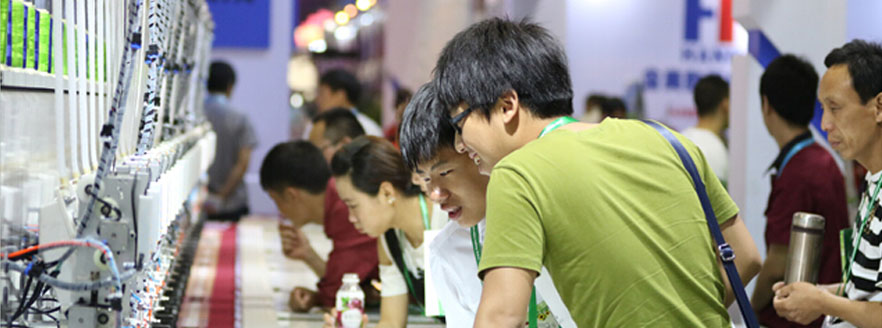
News Center
Speed up the polyester dyeing time
Polyester accounts for more than 50% of the global textile fiber market – no matter the end-use. That’s a lot of polyester needing to be pre-washed, dyed and finished, packed and distributed to customers all around the world. The dye-house manager might confirm that pressure is on to deliver high-quality products while speeding up their processes. Generally, dyeing polyester takes up to 200 minutes including reduction clearing.
Can you speed up, and still reach high quality while saving out on energy, valuable process time and water? We see opportunities to do this in several ways, but the most effective way is probably to reduce polyester dyeing time. When done right, this measure can reduce energy usage by 30%.
The eternal fight against time
The dyeing process of polyester depends on so many variables that it’s impossible to create a one-size-fits-all recipe to speed up dyeing time. Machine type, water quality, dyestuff, auxiliaries, dyeing method, end-use: they all have an impact. Then there’s the influence of the polyester type itself, and the many blends it’s used in.
You’ll understand that 100% polyester responds to dyeing processes differently compared to a blend of polyester or cotton. This is why many dye house managers and technical engineers came up with rules of thumb to make sure absolutely nothing goes wrong, no matter the variables. Very understandable.
It resulted in a dyeing time of around 200 – 220 minutes. First, machines are pre-heated to 40 degrees, where after the polyester product is added and temperature rises one degree per minute. Then, the polyester stays in the machine for another 40-50 minutes.
Stop relying on rules of thumb
It’s safe to say that, in order to speed up polyester dyeing time, we need to let go of rules of thumb. “Instead, focus on your specific situation,” says Harald Gruenewald, Business Development Manager of Classical Textiles at TANATEX Chemicals.
TANATEX Chemicals breaks new ground with ultramodern textile processing solutions, ranging from pre-treatment to finishing. Through a global network of offices, agencies and distributors, it supports their customers worldwide with advanced top quality wet processing products and a high level of technical and tailormade service. For 60 years TANATEX have proven to be a trustworthy and innovative associate.
“Which machines and dyestuff do you use? What type of auxiliaries do you add? Do you work with blends or with 100% polyester?” The answers to these questions help to find the perfect balance between speed and quality, which is different for every dye house.
“To get to this balance, you can’t go around the lab,” explains Harald. “Our lab technicians measure how much time you can save in which phase of the dyeing process.”
The first part of the heating process, for example, is a relatively safe part as colors start to migrate to the fabric around 90 degrees. At 130 degrees, color migration is in full swing, meaning you need to slow down just a little bit to get to evenly spread colors.
“Twenty minutes doesn’t sound like a lot- but it is!”
“If you know exactly how much time you can save out per dyeing cycle and you try it out in real life, you’ll soon realize that lab research pays off,” says Harald. “Let’s say you find out that you can save twenty or thirty minutes per dyed batch, and you do six batches per day on one dyeing machine.
This means you’ll save 120 to 180 minutes per day on one machine, which is between 14 – 21 hours per week and around 56 – 84 hours a month. Think about it: 84 hours less energy and water usage! Not to mention the increase of capacity that this time reduction brings you.
“So, go to the lab and find out how many minutes you can save per cycle,” says Harald. “You’ll be surprised what twenty minutes can do for your business and carbon footprint.”